| Click to Post a New Message!
Page [ 1 ] | | |
|
|
Ballast Weight and Power
It takes power to move ballast weight, but is there any difference for weight carried in loaded tires, wheel weights or raised 3ph? The question came up in a discussion about seats and ride.
I have an impression that rotating weight in wheel weights may reduce working power of a tractor more than comparable weights in loaded tires. It is only an impression, and I'm a long way from my basic physics classes. Almost certainly there's somebody here who has a better grasp on the subject than I do, but here's roughly my impression.
Acceleration takes energy, Changes in velocity or changes in direction are both accelerations. Rotating weight continuously changes direction and has continuous acceleration. Carried weight accelerates only when ground speed changes (unless the tractor turns of course).
It seems like there is at least a component to rotating weight that requires energy. I also know that rotating components such flywheels store energy, which becomes available to support work when engine rpm decreases. So, maybe the tractor does get the energy back that it takes to rotate wheel weights. However, I don't know if it gets all the energy back or if it gets back amounts similar to carried weight. Carried weight also has inertia that tried to keep going when you're trying to stop.
I also don't know if the energy it takes to get rotating and carried weight going or stopping is different and may have different implications for working a tractor. For example, the same inertia that flywheels supply to support rpm in high load conditions also makes it harder to get the rpm back once it's lost. I don't know if rotated or carried weight is any better or worse at this sort of thing. I guess, as advertised, I really can say 'I don't know' a lot. Hope somebody else knows this stuff a bit better.
|
|
Add Photo
Bookmarks: |
|
|
|
Ballast Weight and Power
It would seem to me that we must treat fluid filled tires as a continuously flowing mass, and as such, we must consider the friction created between the fluid and the inside of the tire. I suspect it takes considerable energy to get the mass up to speed, but then less energy to keep it in motion. Sort of like an enclosed paddle wheel system I suppose.
|
|
Add Photo
Bookmarks: |
|
|
|
Ballast Weight and Power
TomG,
Those are some darned good questions, this could be fun!
I have a friend who was involved in a sport that those questions are dealt with in great detail. Tractor pulling.
He competed on the national level for several years, and worked with numorous engineers and other experts on the subject.
His wheel rpm's and surface speed were a little higher than say a 4310 or tc 29, but here is what I learned from him, and all his expeirience and expertese.
You seem to have a good impression on what's going on, and I suspect you have the knowledge to answer your own question and are just looking for a second opinion, "the devil's advocate" so to speak.
Here we go.
It does take energy to rotate ballast, and the rotating ballast does store energy. Liguid ballest does tend to rotate with the wheel some, but not much at low speeds, due to surface tension, and other things to numorous to mention. The problems with liquid ballast have been descussed not only on this forum, but, everywhere else, and I will not bog the conversation down with redundancy.
My friend and his advisors chose to keep the wheel ballast from rotating. They did this by useing bearings on a shaft bolted to the wheels.
The main reason for this was vibration. Believe it or not, a large 30.5X32 tractor tire swith a surface speed in exceess of 60 mph needs to be balanced. 100# wheel weights are poorly balanced when cast, and making steel weights from plate steel wasn't much better. The vibration caused major problems with traction.
Liguid ballast was just to hard to deal with, and getting the exact same weight in each tire is easier said than done. I remeber when they first toyed with the idea of useing liguid, I thought it was promising, a large viscous balancer came to mind, but saftey issues arose from poor weight distribution, and some serious vibration on initial rotation, and it was soon banned in the rulebook.
weight on the 3ph is a good form of ballast for FEL"s or any other fron mounted equipment, but the draft arms are nothing but levers and the rear axle is a fulcrum. any weight at the end of the lever has an effect on the front of the tractor, in other wordS, the more you add to the rear of the hitch, the lighter the front end becomes.
In my humble opinion, the best place for rear balast would be just in front of the rear wheels, you would get alot of benifit from the weight in that location, with little effect on the front end when the loader is not in use. They are easily removed if you would make a bracket and use suitcase weights.
Any body else have any Idea's?
Thanks Tom, this is a fun subject. anything involveing "Newton's Law" always makes for an informative debate, almost as fun as Thermo Dynamic Principles.
You are a huge asset to this board, for a Ford Man......just kidding!!
|
|
Add Photo
Bookmarks: |
|
|
|
Ballast Weight and Power
You guys seem to know what you're talking about here but they're are too many varibles to place weights in one pacific area. Whether it be wheel weights, liquid filled tires or rear ballasts. They all have their own special purpose. And that's my 2 cents worth 
Billy
|
|
Add Photo
Bookmarks: |
|
|
|
Ballast Weight and Power
The ballast installed as pullers do infront of the wheels low to the ground is one of the best places for a drawbar pull. The drawbar pull point is also a point that can change the amount pulled. It is tough to find the ideal place for everything. For normal tractor operation you want 25% ballast on the front of a two wheel drive and on a 4 wheel drive you want 35 to 40% on the front. Four wheel drive with a loader and we try for the 25 to 30% range on the fronts with the load to maxize the balance for traction.
|
|
Add Photo
Bookmarks: |
|
|
|
Ballast Weight and Power
Thanks for the response. Due to me deck BBQ and river day mentioned elsewhere, I'll have to come back to this.
Mark came up with the issue that I intentionally left out at first--fluid dynamics is going to make loaded tires a much more complex system than carried or rotated weight. Unusual behaviour for me; I was trying to simplify things. Tractor pulling, like many competitive things, isn’t simple because little insignificant differences make for winning ways. I hope this subject carries on for a bit. I'm sure I'm going to learn something. I start from virtually zero with tractor pulling so I’m interested in almost everything about it.
Regarding my ability to answer my own question: I have impressions and can generate theory for many things. Real answers I don't have. Maybe that's why I was a semi-pro percussionist for a time. It was easier to pound on my congas than to answer questions that usually resulted in me pounding my head against something. Got paid a little for my efforts too.
|
|
Add Photo
Bookmarks: |
|
|
|
Ballast Weight and Power
Although rotating weight does store energy, I suspect that rotating weight has greater losses that carried weight. I keep thinking that if rotating weight at constant rpm is in acceleration, then the acceleration requires energy that may be 'parasitic' in the sense that it isn't stored in a form that is available to the engine. Of course, I may be missing some basic physics, but maybe carried weight may have less loss than rotating weight.
Loaded tires is a version of carried weight, but I imagine that there are large losses in all the sloshing around that happens, so maybe wheel weights and loaded tires end up with similar efficiency. From comments, from Art’s comment I gather that tractor pullers use neither wheel weights nor loaded tires. Maybe the message is that neither loading nor weights are great. Of course, tractor pullers would be more concerned with traction but power efficiency probably has to be considered for the smaller classes of tractors.
I was looking around on my 1710 for places to hang weight when I was trying to avoid tire loading and wheel weights as well as keep the 3ph for implements. What I noticed is that there's virtually no place to put weight on a tractor that doesn't compromise something. Most places would reduce ground clearance, which is a definite negative for a working tractor. Pulling tractors don’t have that limitation so I imagine that how they are ballasted is the best for both traction and power.
|
|
Add Photo
Bookmarks: |
|
|
|
Ballast Weight and Power
Tom, The wheel weights are the least of all evils here. The tractor pullers have one purpose here and it is hard to compare and shouldn't be but we can learn from that sport.
|
|
Add Photo
Bookmarks: |
|
|
|
Ballast Weight and Power
Art's points are my conclusions as well. For awhile now I've figured out that my applied choice for rear ballast is between wheel weights and 3ph weight. There's really no other place to put it on a working tractor and I never liked the problems that go along with liquid loading. I don't want to tie up the 3ph for ballast, so only the wheels remain.
However, the least of the evils for me seems to be no permanent ballast. I get along fine without additional ballast except for a box scraper when I do heavy loader work, or cement blocks in the bucket when I use box scraper scarifiers or heavy forklift loads. That's my applied solution. I think Art's right that if I wanted something closer to theoretically optimal, I'd look at what tractor pullers do.
|
|
Add Photo
Bookmarks: |
|
|
|
Ballast Weight and Power
Yes, tractor pulling is way complex. And the issues they deal with are somewhat impractical for our uses.
First and foremost is speed. This is an issue I left out of my first reply. I didn't want to make too many comparisons, due to the differences in the two subjects.
In Tractor Pulling, More times than not, he who has the most wheel speed, wins the class, If he can control the tractor well enough to steer it down the track. That is where the subtle differences TomG brought up come into play.
The faster they go, the farther they go. The sooner they get the wheels up to maximum RPMs, at the start, when the transfer sled creats the least amount of resistance, the farther they can go down the track.
Keeping this in mind, along with vibration problems, it is easier to see why avoiding rotating weight on the wheels is the "winner's choice" for ballast.
I've seen several ideas to put ballast on the rear of the tractor,that does not rotate, and does not make the front end lighter.
Mounting wheel weights to the final drive houseings, a shaft with bearings bolted to the rims, and a mid, mount weight bractet are the most widely used
I agree with Art, wheel weights are the least of all evils in our applications. And just like TomG stated, I've stared at my 4300 for hours trying to devise a way to mount suitcase weights just in front of the rear wheels, and can't seem to come up with anything that will give me the clearence I want. I haven't given up yet , but the future seems bleak.
Later Guys!!
|
|
Add Photo
Bookmarks: |
|
| |
|
Page [ 1 ] | | | Thread 39727 Filter by Poster: 2 | 1 | 1 | 1 | 1 | 5 |
|
()
Picture of the Day candoarms
Unanswered Questions
Active Subjects
Hot Topics
Featured Suppliers
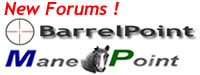
|