| Click to Post a New Message!
Page [ 1 ] | | |
|
|
1200A Secondary Cap Screw
Sorry to post this in Gator forum, but I think the part number is the same for both vehicles. While troubleshooting some wobble in the driven, I noticed the set screw head was not where it should be. After removing unit, I saw the cal screw had brown off in the shaft. I want to extract it, but want to make sure it's left hand thread before I tap it. The parts diagra,s for both gator and 1200a show same part number, but only one has left hand thread in description. I would assume it's LH but thought I might ask here to be sire. Also, does anyone know the length of the screw? And bushing dimensions?
Thanks
coach Larry
|
|
Add Photo
Bookmarks: |
|
|
|
1200A Secondary Cap Screw
|
|
Add Photo
Bookmarks: |
|
|
|
1200A Secondary Cap Screw
The picture looks like an 8mm bolt. They were 8mm up to sn130445 then they went to 10mm. 8mm is a LH thread and that's normally why they are twisted off, 10mm bolts are RH thread. PN 119394 for bolt and PN128560 for bushing if it is 8mm. Same as the early 4x2s.
|
|
Add Photo
Bookmarks: |
|
|
|
1200A Secondary Cap Screw
|
Quote:
The picture looks like an 8mm bolt. They were 8mm up to sn130445 then they went to 10mm. 8mm is a LH thread and that's normally why they are twisted o ...
|
|
Yes, it's 8mm, and sorry for all the typos in my OP. Thanks for deciphering it. Ok, I will tap it and hope I can get it out of there. Thanks again.
|
|
Add Photo
Bookmarks: |
|
|
|
1200A Secondary Cap Screw
I'm not sure if you've tried this yet, but if the bolt broke because of tension and is not bottomed out, you might try a couple of easy tricks. If you know which way the bolt needs to turn to come out, sometimes a pin punch or nail set can be used to dimple what's left of the bolt and turn it until it can be grabbed with pliers. Sometimes it takes surprisingly little torque to tap the bolt around. A little heat to the end of the shaft could help too, as this will increase clearances as the shaft will expand first. Not too much though, as you don't want to ruin temper of shaft or melt seal. Even a bit from a propane soldering torch can help. Another old and useful trick is, when the shaft is hot, hold a bit of beeswax against the stuck bolt or into the bore. It will sweat into the threads and make removal easier regardless of whether tapping with punch or easy out or whatever.
|
|
Add Photo
Bookmarks: |
|
|
|
1200A Secondary Cap Screw
|
Quote:
I'm not sure if you've tried this yet, but if the bolt broke because of tension and is not bottomed out, you might try a pin punch or nail set p. Another old and useful trick is, when the shaft is hot, hold a bit of beeswax against the stuck bolt or into the bore. It will sweat into the threads and make removal easier regardless of whether tapping with punch or easy out or whatever.
|
|
Thanks for your post Trainpilot. I will try using the pin punch trick with a bit of heat. I bought the new Deere cap screw and it has red loctite on it, so might be a little tough if its a stock screw in there. Have never used the beeswax trick; thanks for that. My plan is to drill and tap, using a hex bolt to remove if I cannot do it with the punch..
|
|
Add Photo
Bookmarks: |
|
|
|
1200A Secondary Cap Screw
Good Luck Coach!
I learned the beeswax trick from a retired Granite Construction heavy equipment mechanic. It works surprisingly well--great for frozen studs and such. Consider right-hand or left-hand drills, depending on which way the screw needs to come out. Often times with broken bolts, the drill will bind a bit as it starts to go through the bolt and will spin the bolt out. So you want to use a lh bit to extract rh screws and rh bits to extract lh screws. Of course if the bolt is bottomed out hard or loctited in it gets more difficult.
|
|
Add Photo
Bookmarks: |
|
|
|
1200A Secondary Cap Screw
Unfortunately, I broke my first tap while nearly done tapping a 6/32 thread. Now I have an 8mm LH bolt with a broken 6/32 hardware-store (junk) tap broken off just below the surface. I really don want to take the transaxle off the machine if I can help it, but not sure I can get this little tap out. Big bummer..
|
|
Add Photo
Bookmarks: |
|
|
|
1200A Secondary Cap Screw
I've been down that road a few times myself. Have you got an oxy/actelylene set? If the tap is broken below hole you drilled into original bolt, you might be able to put on your smallest tip and heat just the tap. Put the flame into one flute and let it out other. If you can get it red hot and let it cool down slowly, it'll lose its temper, and drilling will be much easier. Your initial hole should help keep drill centered. I'd go for a carbide, or the best bit you can find, bigger than before, and try drilling again. Have you ever used a Helicoil? They will let you drill out original hole oversize, then tap and screw new threads into bore. In the end, the broken bolt mostly just keeps clutch onto splined shaft. You could also drill bigger and tap for 10mm.
|
|
Add Photo
Bookmarks: |
|
|
|
1200A Secondary Cap Screw
Mapp gas is the hottest I have on site, and the tip is just a standard soldering tip. I suppose I can try to be precise and hopefully make it brittle enough to punch or drill. If that doesn't work, I'll try a carbide bit and increase to 8/32. Should I go dry or wet n drilling new hole with tap in. Other than that, looks like a long day of taking transaxle off and putting the shaft in the mill.
|
|
Add Photo
Bookmarks: |
|
| |
|
Page [ 1 ] | | | Thread 195031 Filter by Poster: 10 | 1 | 5 |
|
()
Picture of the Day dododo
Unanswered Questions
Active Subjects
Hot Topics
Featured Suppliers
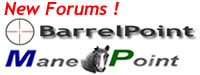
|